The Essential Role of Welding Examination: Understanding the Procedures, Tools, and Standards That Govern Quality Assessment in Welding Procedures
Welding assessment is a vital part of top quality guarantee in welding procedures, ensuring the architectural stability and security of welded assemblies. Recognizing the interplay between assessment approaches and governing conformity increases crucial concerns about the obstacles faced in maintaining these necessary procedures.
Importance of Welding Inspection
Welding examination is critical in guaranteeing the stability and safety and security of welded structures, as it frequently functions as the last checkpoint prior to parts are taken into service. The relevance of this inspection hinges on its capacity to identify prospective issues that might jeopardize the efficiency and durability of welded joints. Offered the high stakes entailed, particularly in fields such as building and construction, aerospace, and auto, extensive inspection processes are important.
Welding flaws can develop from numerous elements, including incorrect techniques, insufficient tools, or improper products. Failing to identify these problems can bring about disastrous consequences, consisting of architectural failures, which might result in injury, loss of life, and considerable financial obligations. Welding examination gives a methodical technique to evaluate the top quality of welds, making certain compliance with industry standards and governing demands.
Moreover, reliable welding evaluation contributes to boosting total performance by decreasing rework and ensuring that tasks remain on routine. By cultivating a society of high quality guarantee, organizations can additionally enhance their track record and client depend on. Essentially, the significance of welding evaluation can not be overemphasized, as it plays a crucial role in safeguarding both human lives and investments in framework.
Secret Examination Treatments
A comprehensive method to inspection treatments is vital for making sure the high quality and integrity of welded joints. Effective inspection starts with pre-weld assessments, that include assessing welding specifications, material residential properties, and joint layouts to recognize prospective difficulties. This prep work stage establishes a baseline for high quality assumptions.
During the welding procedure, in-process examinations are essential. Assessors keep an eye on specifications such as warm input, traveling rate, and electrode angle to make sure conformity with well-known requirements. Visual inspections are the very first line of defense, making it possible for the identification of surface area problems, such as fractures, porosity, or insufficient combination.
Post-weld assessments involve advanced methods to evaluate the stability of the joint. This might include non-destructive screening (NDT) techniques such as ultrasonic testing, radiographic testing, or magnetic bit testing. These strategies supply much deeper insights into the internal framework of the weld, revealing possible defects that may not show up externally.
Documents plays an important function throughout the examination process. Comprehensive records of assessments, including findings and rehabilitative actions, guarantee traceability and liability, inevitably adding to continuous enhancement in welding methods and overall quality control.
Crucial Equipment for Inspection
Effective assessment relies upon making use of specific tools made to evaluate the high quality and honesty of welded joints. Secret tools in this process consist of aesthetic examination devices, such as magnifying borescopes and glasses, which permit assessors to recognize surface area issues and abnormalities. In addition, ultrasonic screening (UT) devices plays a critical duty by utilizing high-frequency acoustic waves to find inner imperfections within welds, making certain that hidden weaknesses are determined before they bring about failure.
Radiographic testing (RT) is another necessary method, utilizing X-rays or gamma rays to produce pictures of the welds, disclosing interior issues that may not be visible through other inspection techniques - Houston Welding Inspection. Magnetic particle testing (MT) is employed for ferromagnetic materials, enabling examiners to find surface and near-surface issues by applying fine bits and magnetic fields
Dye penetrant screening (PT) is also considerable, including the application of a fluorescent dye to disclose surface cracks and gaps. Each of these techniques and devices adds to a comprehensive assessment strategy, making certain blog that bonded structures fulfill the required quality requirements and continue to be secure for usage in their corresponding applications.
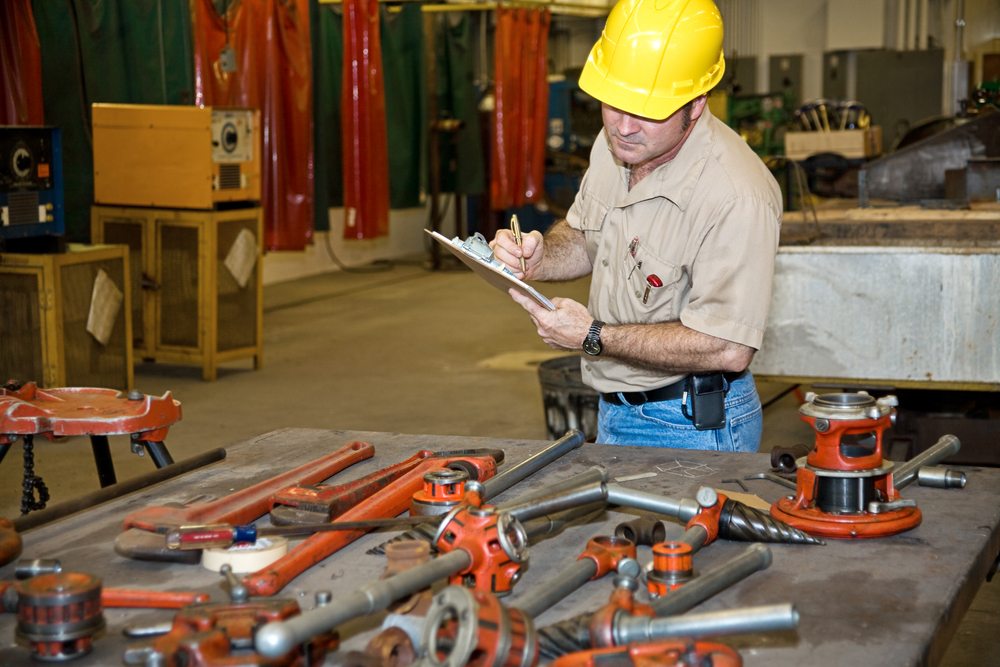
Industry Criteria and Rules
Quality control in welding evaluation is substantially affected by sector requirements and regulations that regulate techniques and make sure safety and security. These requirements function as standards for quality, detailing the necessary methods for assessment, testing, and documents. Trick organizations such as the American Welding Culture (AWS), the American Culture of Mechanical Engineers (ASME), and the International Organization for Standardization (ISO) establish guidelines that welding professionals have to adhere to throughout the examination process.
Conformity with these standards is not only a matter of regulatory obligation yet also a vital part of risk administration in welding operations. They encompass various facets, including material option, welding strategies, and certifications of workers. AWS D1.1 details structural welding needs, while ISO 3834 defines high quality requirements for welding procedures.
Furthermore, market policies dictate the essential qualifications for welding assessors, demanding qualifications that verify their competence. This positioning with requirements makes sure that assessments are performed regularly and properly, inevitably protecting the stability of bonded structures. Complying with these market criteria and guidelines is extremely important in promoting operational efficiency and keeping public rely on welding techniques.
Obstacles in Welding Inspection
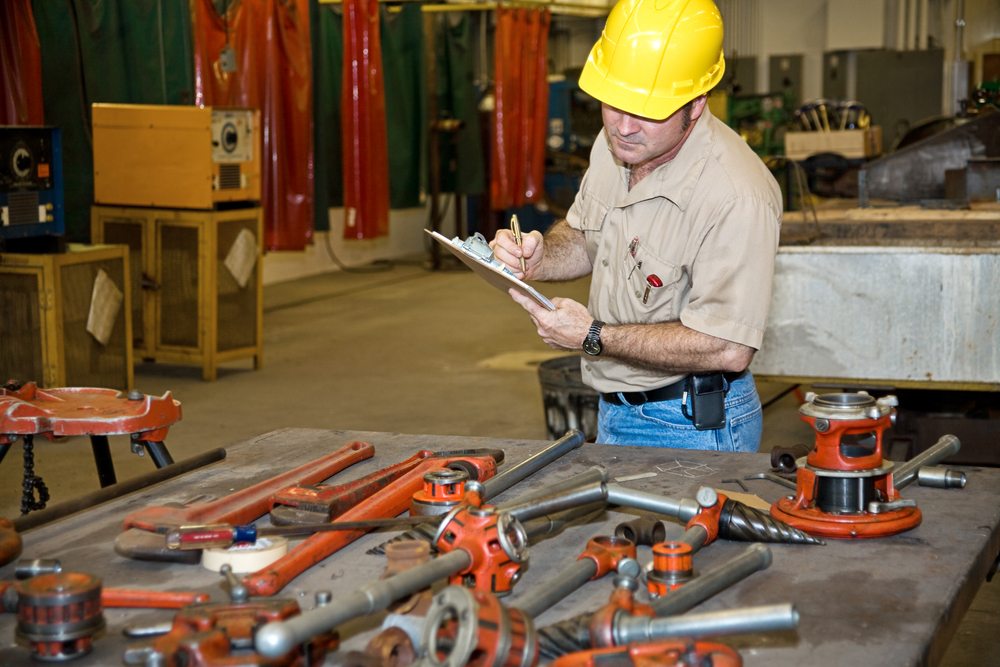

Welding inspection deals with numerous challenges that can impact the reliability and security of bonded frameworks. One significant challenge is the intricacy of the welding refines themselves, which can vary greatly depending upon products, joint configurations, and environmental problems. This variability demands a detailed understanding of varied inspection methods and their ideal applications.
An additional challenge exists in the progressing nature of welding modern technology. As brand-new products and approaches are presented, inspectors must constantly update their knowledge and skills to properly review the top quality of welds. In addition, the physical availability of weld areas can hinder evaluation efforts, particularly in restricted or high-risk atmospheres.
Moreover, human elements play a critical role in welding examination. Houston Welding Inspection. The subjective nature of aesthetic assessments can lead to variances, as different inspectors might interpret the same weld in a different way. This highlights the importance of standard training and qualification for inspectors to make sure a consistent approach to high quality evaluation
Finally, the integration of sophisticated modern technologies, such as automated assessments and fabricated intelligence, presents both difficulties and chances. While these modern technologies can enhance precision and effectiveness, they additionally call for significant investment and experience to implement efficiently. Addressing these obstacles is essential for keeping the integrity of look at here now bonded structures.
Final Thought
Welding examination is vital for making sure the security and honesty of bonded frameworks. Through strenuous assessment treatments, the usage of specialized equipment, and adherence to acknowledged sector criteria, the quality of welding procedures can be systematically assessed. Obstacles persist in the evaluation procedure, yet the execution of efficient techniques can reduce threats related to structural failures. Inevitably, a robust welding examination framework not only ensures conformity with regulations but also boosts total functional efficiency and dependability.
Welding assessment is a crucial part of quality assurance in welding operations, ensuring the architectural stability and security of bonded assemblies.Welding evaluation is essential in guaranteeing the integrity and security of welded structures, as it frequently offers as the final checkpoint prior to components are placed right into service. Welding evaluation supplies go to these guys a methodical strategy to review the quality of welds, guaranteeing compliance with sector standards and governing demands.
Quality assurance in welding evaluation is considerably affected by industry criteria and guidelines that govern techniques and guarantee safety. Key companies such as the American Welding Society (AWS), the American Culture of Mechanical Engineers (ASME), and the International Organization for Standardization (ISO) develop guidelines that welding specialists need to adhere to throughout the evaluation procedure.